- Biochemia
- Biofizyka
- Biologia
- Biologia molekularna
- Biotechnologia
- Chemia
- Chemia analityczna
- Chemia nieorganiczna
- Chemia fizyczna
- Chemia organiczna
- Diagnostyka medyczna
- Ekologia
- Farmakologia
- Fizyka
- Inżynieria środowiskowa
- Medycyna
- Mikrobiologia
- Technologia chemiczna
- Zarządzanie projektami
- Badania kliniczne i przedkliniczne
Metody zestalania odpadów wysokoaktywnych
a. Wypalanie w pojemniku
b. Zestalanie rozpyłowe
c. Zestalanie w szkle fosforanowym
d. Wypalanie fluidyzacyjne
Wszystkie te procesy obejmują wysokotemperaturowe ogrzewanie (400˚C - 1200˚C), które oczyszcza próbkę ze względnie lotnych związków i pozwala na otrzymanie ciała stałego (często stopu). Ochłodzony materiał jest względnie stabilny chemicznie ( w temperaturze niższej niż proces w jakim uczestniczył).
Chemia zestalania
Materiał wypalony jest mieszaniną, w skład, której wchodzą nielotne tlenki, siarczany oraz fosforany metali. Wszystkie inne składniki ulegają utlenieniu. Zestalanie (otrzymywanie stopów) prowadzi zawsze do wprowadzania związków obojętnych chemicznie co może zwiększyć masę odpadów nawet czterokrotnie. Warunkiem wykorzystania zestalania jako metody przetwarzającej wysokoaktywne odpady jest zawartość 70% molowych substancji chemicznych, które przejdą ma materiał topliwy w temperaturach poniżej 1000˚C.
Jako substancje, które nasilają właściwość topliwości tzw. Topniki stosuje się:
• Fosforany [1, 2, 3]
• Borofosforany [4, 5, 6]
• Krzemiany [6, 7]
• Borokrzemiany [4, 7, 8]
• Borany [9]
Przed tworzeniem postaci stopu, należy poznać dokładny skład odpadów wysokoenergetycznych. Dopiero wtedy można określić prawidłowy proces stapiania, który jest inny w zależności od składu chemicznego. Istnieją komponenty, które ułatwiają wytworzenie właściwości topliwych np. kationy żelaza, sodu i glinu [10]. Utrudnieniem jest również obecność jonów siarczanowych, które są nie stabilne w wysokich temperaturach (>700˚C), gdyż ulegają utlenieniu. Obecność ich często wymaga dodawania innych komponentów np. wapnia. Bardzo trudne wytworzenie jest stopów w temp. 850˚C - 900˚C [1]. Niecałkowite reakcje utlenienia prowadza do przyśpieszonej korozji układów np. korozja układu odprowadzającego gazy. W szczególnych przypadkach siarczany prowadzą do powstawania osadów ciężkich [11]. Fluorki pozostawiane są w procesie stapiania [12]. W wysokich temperaturach fluorki przechodzą w postać gazową, stąd też system ich zawracania lub usuwania inna metodą. Fluorki, podobnie jak siarczany powodują korozję układów metalowych szczególnie, gdy występują w stężeniach powyżej 0,001M. Możliwy jest wtedy proces korozji stali nierdzewnej jak i stali tytanowej. Aby zapobiec tym efektom ubocznym stosuje się metodę kompleksowania metalami np. cyrkonem.
Oprócz anionów, ważnym elementem składowym są również metale takie jak rtęć, czy ruten. Rtęć jest usuwana z odpadów wysokoaktywnych, gdy przeróbka ich to postaci stopu zachodzi w temperaturze powyżej 400˚C. Rtęć tworzy wtedy tlenki które w temperaturze ok. 350˚C zaczynają kondensować zatykając elementy konstrukcji. Metodę usuwania rtęci z odpadów wysokoaktywnych przedstawiono w [13]. Metalem, który niemal zawsze towarzyszy odpadom wysokoaktywnym i ich przeróbce jest ruten. Metal ten może ulegać wielu różnym procesom. Najczęstszym bo aż 80% rutenu ulega utlenieniu tworząc zestalające się osady zatykające układ. Dlatego do układu wprowadza się czynniki, które zmniejszą proces utleniania nawet do 1% rutenu.
Wypalanie w pojemniku
Proces wypalania w pojemniku jest procesem prostym, periodycznym, może być stosowany na szeroka skalę nie zależnie od masy zasilającej [14]. Jednak ma także wady np. wymaga stosowania pojemników ze stali nie rdzewnej oraz niskiej przewodności stopu. Pojemnik użyty do spalania jest również ostatecznym pojemnikiem stopu. Proces ten polega na tym, iż ciekłe odpady są dostarczane do pojemnika, który ma możliwość grzania i chłodzenia. Pierwszym etapem jest zatężanie w stałej objętości, do momentu pojawienia się na ścianach pojemnika wyprażonego materiału. Druga faza to gromadzenie się na ścianach pojemnikach znacznych ilości wyprażonego materiału, który redukuje przewodnictwo ciepła ze ścianek do wyprażanych odpadach. To przewodnictwo cieplne umożliwia zmniejszenie dostarczanego ciepła. Kolejnym etapem jest wyprażenie maksymalnej ilości odpadów i niewielkiej ilości cieczy (stożek w górnej części wyprażonego materiału głębokości do 1m). Faza kolejna to całkowite odparowanie cieczy oraz prażenie pojemnika w temperaturze 850˚C - 900˚C, co pozwala na usunięcie wszystkich lotnych składników. Ostatnim etapem jest ponowne schłodzenie pojemnika i jego zawartości, i skierowanie go składowania.
Pojemniki użyte w procesie wypalania muszą spełniać konkretne warunki:
• Pojemniki muszą być zaopatrzone w urządzenia do pomiaru poziomu cieczy i temperatury
• Termopary [10, 11, 13, 15]
• Trójstopniowa redukcja temperatury pieca, regulowana temperaturą wnętrza i ścian pojemnika [11] –
zapobiega to niekontrolowanemu utlenianiu się wysokoaktywnych odpadów i nadmiernej korozji pojemnika.
Należy zwrócić uwagę, iż zwiększanie wielkości pojemnika ma niewielki wpływ na wzrost wydajności. Maksymalna szybkość odparowywania jest limitowana przez zasilanie w górnej części pojemnika lub przez przekrój poprzeczny pojemnika.
Obecnie przyjmuje się, że proces wypalania w pojemniku ma trzy główne etapy [16]:
1. Zasilanie i zatężanie, przy stałej szybkości dozowania
2. Tworzenie warstwy zbitego osadu i jego wyprażanie, ze stopniową redukcją zasilania
3. Wyprażanie po wstrzymaniu zasilania, ogrzewanie materiału 850˚C - 900˚C oraz ochładzanie w celu
usunięcia pojemnika i jego składowania.
Czas trwania poszczególnych etapów jest różny. Przybliżone czasy zostały przedstawione w tabeli 1 dla pojemnika o ogrzewaniu wewnętrznym 5kW. Czas trwania ogrzewania wydłuża się, jeśli materiał odparowywany posiada nawet niewielkie ilości substancji pianotwórczych.
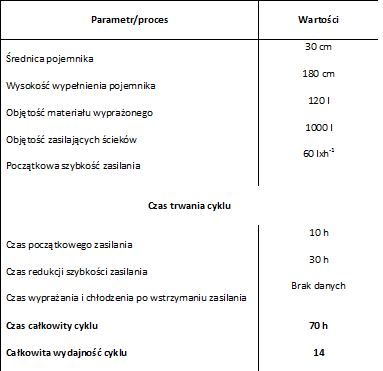
Tabela 1. Czas trwania poszczególnych cykli oraz ich wydajności w procesie wyprażania w pojemniku o ogrzewaniu wewnętrznym 5kW [16]
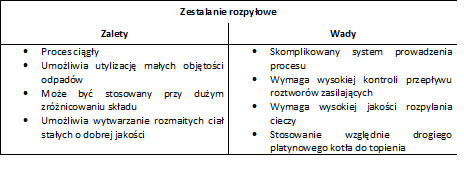
Topielnik pozwala usunąć małe ilości wody i azotanów, pozostałe składowe tworzą stop. Ze względu na obecność fosforanów, pojemnik może być wykonany jedynie z platyny, która oprze się korozji katalizowanej przez fosforany. Obecnie wiadomo, że dobre rezultaty do temperatury 1000˚C przynosi stosowanie stopów chromu i niklu 1:1, a stop ceramiczny (glinowo-chromowy) wytrzymuje temperaturę do 1100˚C. Wydajność platynowego topielnika wynosi 1,7l stopionego materiału na godzinę, dla pojemnika o średnicy 25 cm i wysokości sekcji ogrzewanej 35 cm [9].
Zestalanie w szkle fosforanowym
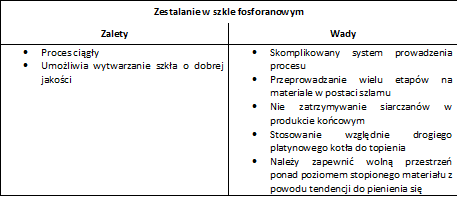
Całkowita wydajność, dla pojemnika o średnicy 25 cm, wysokości grzewczej 65 cm, wynosi 1,4 lxh-1 w przeliczeniu na wytworzone szkło. Pojemnik odbierający powstałe szkło jest zbliżony do pojemnika składowego w metodzie zestalania rozpyłowego.
Zestalanie fluidyzacyjne
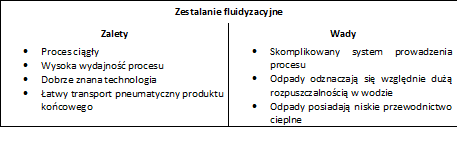
Tabela 3. Wady i zalety zestalania fluidyzacyjnego ciekłych odpadów wysokoaktywnych
1. Małe – o średnicy poniżej 30cm – ogrzewane są przez ścianki reaktora [20, 21]
2. Średnie i duże reaktory – posiadają instalację dodatkowego wewnętrznego ogrzewania.
Dobranie odpowiedniego ogrzewania jest ważne w celu uniknięcia przegrzań lokalnych lub zbrylania się [20, 22 , 23]. Podczas zestalania odpadów wysokoaktywnych o dużej prędkości samoogrzewania się stosuje się instalacje posiadające dodatkowe systemy chłodzące.
Istnieją cztery główne metody zestalania odpadów wysokoaktywnych. Z każdym rokiem zwiększa się optymalizacja każdej z tych metod i jej użytkowość. W tym przypadku nauka i technologia działają wspólnie co pozwala na otrzymywanie stopów o pożądanych właściwościach [24].
Autor: Karolina Wójciuk
Literatura
[1] Barton G.B., Weed J.A. Solidification of High-Level Wastes. Part V. A Factorial Study of the Effect of Varying the Concentration of the Components of Purex-Type Waste on the Properties of Phosphate Solids, Appendix. Response Surface Statistical Analysis. USAEC Report BNWL-544, Battelle – Northwest. 1968
[2] Barton G.B. Solidification of High Level Walters. Part IV. Phosphate Melts for Fixation of Radioactive Residues form Purex – Type Wastes. Three to Fifty Percent Fission-Product Oxides. USAEC Report BNWL-80. Battelle – Northwest 1965
[3] Mendel J.E., Rey G., McElroy J.L. Design Verification Testing of Waste Solidification Processes, in Proceedings of the Symposium on the Solidification and Long-Term storage of Highly Radioactive Wastes. Richland Wash., Feb. 14 – 18. 1966: Regan W. H. (Ed.) USAEC Report CONF – 660208, pp. 513 -515 1966
[4] Barton G.B. Solidification of High Level Walters. Part VI. Mixed Phosphate, Borate, Silicate Melts for Fixation of Purex – Type Wastes. USAEC Report BNWL-373. Battelle – Northwest 1967
[5] Mendel J.E. Preparation of Melts from Solidified Waste, In Quarterly Progress Report, January – March 1965. Resarch and Development Activities Fixation of Radioactive Residues: Platt A. M. (Ed.), USAEC Report BNWL-76 Battelle-Norhwest. 1965
[6]Clark W.E., Godbee H.W. Fixation of Simulated Highly Radioactive Wastes in Glassy Solids, in Treatment and Storage of High-Level radioactive Wastes. Symposium Procedings. Vienna 1962 pp. 411-439. International Atomic Energy Agency Viennna 1963
[7] Bonniaud R. Survey of the Studies Conducted In France on the Solidification of Concentrated Fission-Product Solution, In Proceedings of the Symposium on the Solidification and Long-Term Storage of Highly Radioactive Wastes, Richland, Wash., Feb. 14-18. 1966: Regan W.H. (Ed.) USAEC Report CONF-660208, pp. 120-139. 1966
[8] Mendel J.E. Battelle – Northwest, personal Communications with K.J. Schneider. 1970
[9] Kaser J.D., Moore J.D. The Development of Spray Calciner – Melter, in Proceedings of the Symposium on the Solidification and Long-Term Storage of Highly Radioactive Wastes, Richland, Wsh., Feb. 14 -18: Regan W.H. (Ed.) USAEC Report CONF-660208 pp.326-374 1966
[10] Blasewitz A. G. Mendel J E., Schneider K.J., Thompson R.J. Interim Status Report on the Waste Solidification Demonstration Program, USAEC Report BNWL-1083 Battelle-Northwest. 1969
[11] McElroy J.L, Cooley C.R., DeMier W.V., Mendel J.E. Waste Solidification Program, Vol. 4, Pot Calciner Performance During the First Radioactive Tests in WSEP, USAEC Report BNWL-814, Battelle-Northwest 1968
[12] Petrie, Bailey E.J., Rhodes D.W., Legler B.M. Fluidized-Bed Calcination of Simulated Ziroconium Fluoride Wastes in Exploratory Pilot Plant Tests. USAEC Report IDO-14653. Phillips Petoleum Company. 1965
[13] Clark W.E., Fitzgerald C.L. Proposed Means for the Removal of Mercury from Radioactive Waste Solutions, USAEC Report ORNL-TM-827. Oak Ridge National Laboratory 1964.
[14] Clark W.E. et al., Development of Processes for Solidification of High-Level Radioactive Wastes: Summary for Pot Calcination and Rising Level Potglass Processes, USAEC Report ORNL-TM-1584, Oak Ridge National Laboratory 1966
[15]Schneider K.J. (Ed.) Waste Solidification Program, Vol. 1 Process Technology: Pot, Spray, and Phosphate Glass Solidification Processes, USAEC Report BNWL-1073, Battelle-Northwest 1969.
[16] Schneider K.J. Zestalanie i usuwanie wysokoaktywnych odpadów promieniotwórczych. Ośrodek Informacji o Energii Atomowej. Seria: Ochrona przed promieniowaniem Nr66 (524) 1972
[17] Bond W.R., Development Spray Calciner Runs, In Quarterly Progress Report, Research and Development Activities, Fixation of Radioactive Residues. 1967 w Platt A.M. (Ed.), USAEC Report BNWL-677 Battelle – Nortwest. 1968
[18] Strickland G, Tuthill E.J., Drager R.F. Phosphate Glass Process: Evaporator Studies with Simulated Purex Wastes, in Prceedings of the Symposium on Solidiification and Long-Term Storeg of Highly Radioactive Wastes, Richland, Wash., Feb. 14-18.1966, w Regan W.H. (Ed.), USAEC Report CONF-660208 pp.280-300 1966
[19] Modrow R.D., Lakey L.T. Removal of Particulates from Waste Calcining Facility Off-Gas, USAEC Report IDO-14607, Phillips Petroleum Company. 1964
[20] Lakey L.T., Lohse G.F., Palica W.P. Development of Fluidized-Bed Calcination Facility, USAEC Report IDO-14608, Philips Petroleum Company 1965
[21] Loeding J.W., Carls E.J., Anstasia L.J., Jonke A.A. The Fluid-Bed Calcination of Radioactive Waste. USAEC Report ANL-6322, Argonne National Laboratory, 1961
[22] Alford M.D. Fluidized-Bed Calcination of Simulated Purx High-Activity Level Wastes, Interim Report, USAEC Report HW-66384-RD, General Elektric Company 1960
[23] Shneider K.J. Fluidized-Bed Calcination Studies with Simulated ICPP Waste Solution, USAEC Report HW-65838-RD, General Electric Company 1960
[24] Wójciuk K. Własności zestalonych odpadów. Labro Technology. 2013
Tagi: lab, laboratorium, biotechnologia, zestalanie odpadów wysokoaktywnych, chemia zestalania, wypalanie w pojemniku, zestalanie rozpyłowe, zestalanie w szkle fosforanowym, wypalanie fluidyzacyjne
wstecz Podziel się ze znajomymi
Recenzje