Wysokowydajne narzędzia przemysłowe na bazie diamentów
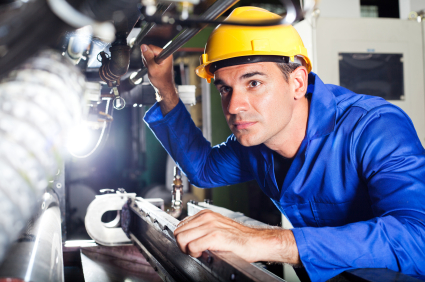
Paradoksalnie jednak to ich ogromna twardość – cecha która przesądza o tym, że diamenty przemysłowe są tak nieocenione – stwarza niezmiennie problem przy opracowywaniu kolejnej generacji wysokowydajnych narzędzi. Uzyskanie precyzyjnych i złożonych, swobodnych geometrii i struktur 3D z diamentów przemysłowych i innych ultratwardych materiałów jest niezwykle trudne technicznie. Dofinansowany ze środków UE projekt DIPLAT, nad którym prace rozpoczęły się w styczniu 2013 r., ma zająć się tym problemem, zapoczątkowując przełom technologiczny na bazie laserów.
Dzięki temu przemysł europejski będzie mógł w pełni wykorzystać rozwijający się rynek wysokowydajnej obróbki skrawaniem i oprzyrządowania. Istnieje nadzieja, że partnerzy projektu, który otrzyma łącznie 3,2 mln EUR dofinansowania ze środków UE, otworzą nowe możliwości w zakresie projektowania wysokowydajnych narzędzi.
W ten sposób wysoce wyspecjalizowane MŚP europejskie z sektora oprzyrządowania i obrabiarek zyskają wyraźną przewagę konkurencyjną.
DIPLAT ma okiełznać potencjał laserów impulsowych o krótkich i ultrakrótkich impulsach oraz wysokiej jasności. Ta technologia oprzyrządowania zostanie oparta na ablacji 3D laserem impulsowym (PLA), a opracowana i demonstrowana będzie w różnorakich kontekstach zastosowań przemysłowych. Ablacja laserowa to proces polegający na usuwaniu materiału z powierzchni ciała stałego poprzez napromienianie jej wiązką laserową w celu uzyskania gładszej i wyraźniej zarysowanej krawędzi.
Jednym z materiałów, nad którym pracują partnerzy projektu, jest polikrystaliczny diament (PCD). Ten materiał wykazuje zazwyczaj odporność na ścieranie nawet 500 razy wyższą od węglika spiekanego, a także charakteryzuje się wysoką przewodnością cieplną, która umożliwia odprowadzanie ciepła z krawędzi skrawającej, co pozwala zapobiegać szybkiemu zużywaniu się narzędzi. Produkty PCD znajdują szerokie zastosowanie w przemyśle motoryzacyjnym, lotniczym, elektronicznym, drzewnym i optycznym.
Materiały PCD o większych kryształach wykazują wyższą odporność na ścieranie, ale krawędź skrawająca jest bardziej chropowata. Mniejsze kryształy zapewniają co prawda ostrzejszą krawędź skrawającą, ale przy krótszej trwałości narzędzia.
Regularny azotek boru (CBN) to kolejny (drugi pod względem twardości po diamencie syntetycznym) ultratwardy materiał stosowany jako ścierniwo. Jedną z fizycznych zalet CBN w porównaniu do tradycyjnych materiałów ściernych jest, prócz wyższej twardości w temperaturze otoczenia, utrzymywanie tej twardości w szerokim zakresie temperatur.
Celem partnerów projektu DIPLAT jest zapewnienie producentom narzędzi możliwości projektowania z tych materiałów wysoce specyficznych powierzchni funkcjonalnych (o kontrolowanej mikrogeometrii), aby tworzyć dokładnie takie wysokowydajne narzędzia, na jakie jest zapotrzebowanie. Partnerzy projektu, który ma się zakończyć w lipcu 2016 r., zademonstrują wówczas wyższą wydajność i funkcjonalność tych nowych narzędzi na przykładzie wymagających zastosowań przemysłowych.
Projekt DIPLAT położy podwaliny pod nowatorską technologię oprzyrządowania i pomoże wprowadzić europejski sektor produkcji do awangardy wysokowydajnej obróbki skrawaniem. Dzięki temu użytkownicy końcowi zyskają wyższą funkcjonalność i znakomitą wydajność maszyn, co ostatecznie wzmocni konkurencyjność Europy.
Więcej informacji:
DIPLAT
www.fp7-diplat.eu/
Źródło: www.cordis.europa.eu
Tagi: laser, diament, narzedzia, projekt, przemysl
wstecz Podziel się ze znajomymi