Diamentopodobne powłoki zapewniające oszczędność paliwa
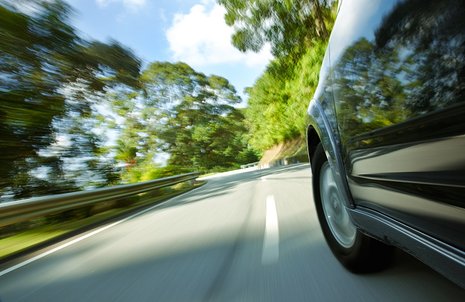
Powłoki oparte na węglu są już używane w produkcji masowej. Obecnie zespół naukowców IWS prowadzony przez prof. Lesona, dra Hansa-Joachima Scheibego i dra Volkera Weihnachta osiągnął sukces w produkcji wolnych od wodoru powłok ta-C w skali przemysłowej ze spójnym poziomem jakości. Te czworościenne amorficzne powłoki węglowe są znacznie twardsze i przez to bardziej odporne niż konwencjonalne powłoki diamentopodobne. „Niestety nie wystarczy zdrapać pył diamentowy i osadzić go na komponencie. Zostaliśmy zatem zmuszeni do poszukania innej metody”, powiedział dr Scheibe, który poświęcił ponad 30 lat na badania nad redukcją właściwości ciernych węgla.
Laser impulsowy kontroluje łuk świetlny
W sposób podobny do staromodnych projektorów filmowych metoda łuku laserowego generuje łuk między anodą i katodą (węglem) w próżni. Łuk jest inicjowany przez impuls laserowy na węglowym elemencie docelowym. Powoduje to wyzwolenie plazmy składającej się z jonów węgla, która osadza się w postaci warstwy na elemencie roboczym w próżni. Aby uruchomić ten proces w skali przemysłowej, laser impulsowy jest skanowany w pionie w obracającym się cylindrze grafitowym jako metoda kontrolowania łuku. Cylinder jest konwertowany równomiernie na plazmę dzięki ruchowi skanującemu i obrotom. Aby zapewnić równomiernie gładką powłokę, pole magnetyczne prowadzi plazmę i odfiltrowuje cząsteczki kurzu.
Metoda łuku laserowego może posłużyć do układania bardzo grubych powłok ta-C do 20 mikrometrów z dużym tempem powlekania. „Duża grubość powłoki jest bardzo ważna w określonych zastosowaniach – w szczególności w branży motoryzacyjnej, gdzie komponenty są przez długi czas poddawane ogromnym obciążeniom”, powiedział dr. Weihnacht.
Producent samochodów i motocykli BMW pracuje intensywnie nad wdrożeniem komponentów silnika ta-C w skali przemysłowej w różnych modelach swoich pojazdów, czego celem jest zmniejszenie zużycia paliwa. Prof. Leson widzi w tym pierwszy poważny krok w zastosowaniu metody łuku laserowego do oszczędzania zasobów. Prywatnie jest miłośnikiem motocykli i dostrzega również kolejny pozytywny efekt płynący z tego rozwiązania: „Fakt, że nasze badania zwiększają przyjazność motocykli dla środowiska sprawia, że czuję się rozgrzeszony za każdym razem, kiedy wybieram się na przejażdżkę”, powiedział, nie kryjąc uśmiechu.
Źródło: http://www.nanowerk.com/news2/green/newsid=40355.php
Tagi: powloka, wegiel, diament, paliwo
wstecz Podziel się ze znajomymi